Client Background
Our client is a design-driven urban infrastructure company that we have worked with for nearly 15 years. During this time, we have liaised closely with them to design, prototype and mass manufacture an urban cycle parking product. A design that is robust, secure, and stands the test of time. The product is now sold around the UK, Europe and the US.
Client Brief
Several years ago, our client began to see orders accelerate from 10-15 units per month to 50-75 units a month. This required a complete overhaul of manufacturing and quality assurance processes. This would account for a 10x increase in the number of monthly parts shipped.
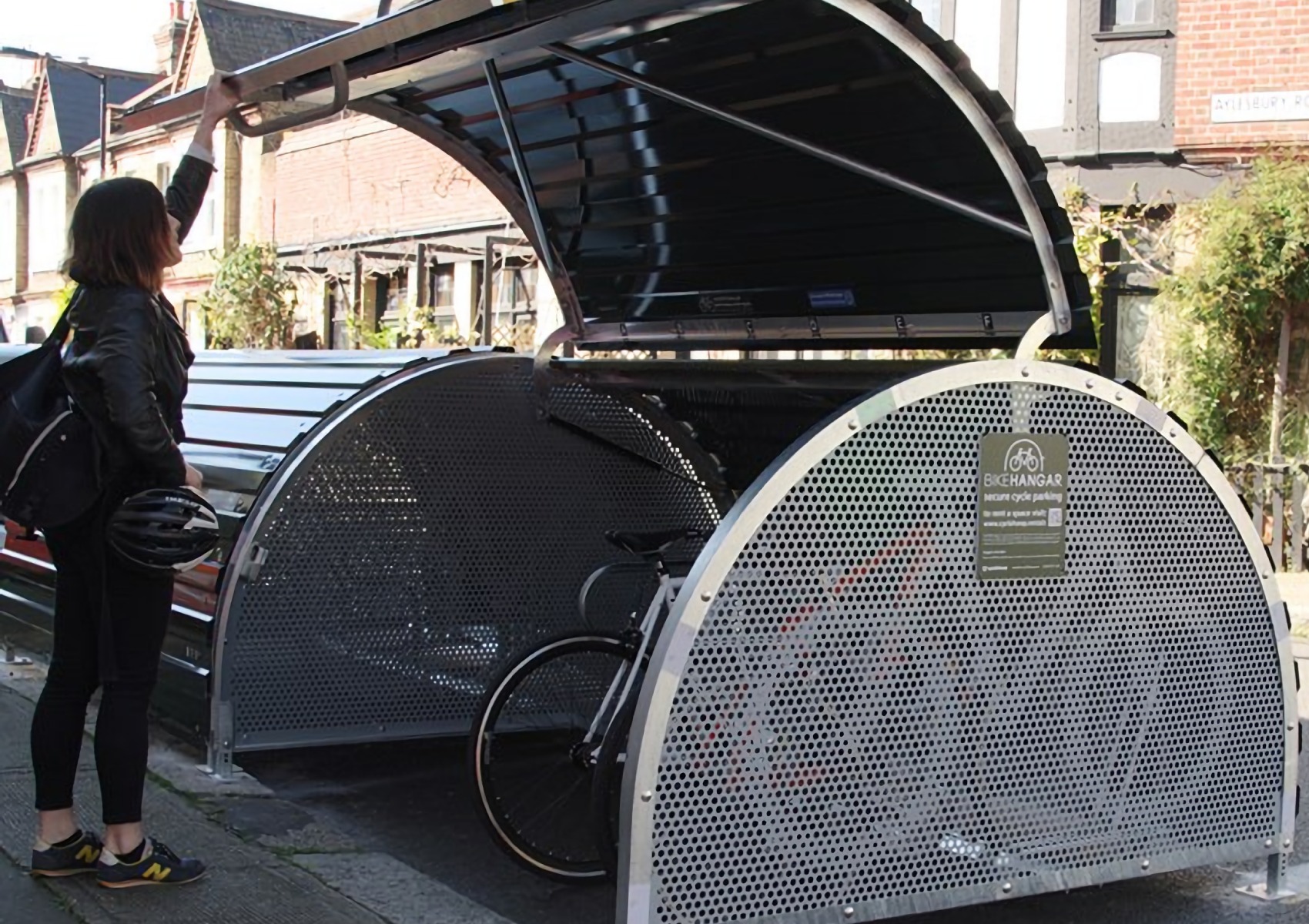
DESIGN FOR MANUFACTURE
Over a twelve-month period, we made several key capital investments, were involved in design changes, and modified some manufacturing processes. This enabled us to supply in volume and maintain the same high-quality standards.
For example, in 2020 we moved most of the MIG welding to our industrial robotic welding system which allowed us to offer greater consistency across batches and better manage production scheduling. Our improved processes and attention to detail supported a ten-fold increase in production and yielded nearly 10% cost savings on each assembled unit.
DESIGN FOR MANUFACTURE AND ASSEMBLY
We worked with our client to introduce specialist tooling and fixtures to speed up processes and ensure quality would be maintained regardless of the increase in volume of parts produced.
Robotic welding was introduced for nearly all fabricated assemblies, which smoothed out production planning and ensured a high-quality standard.
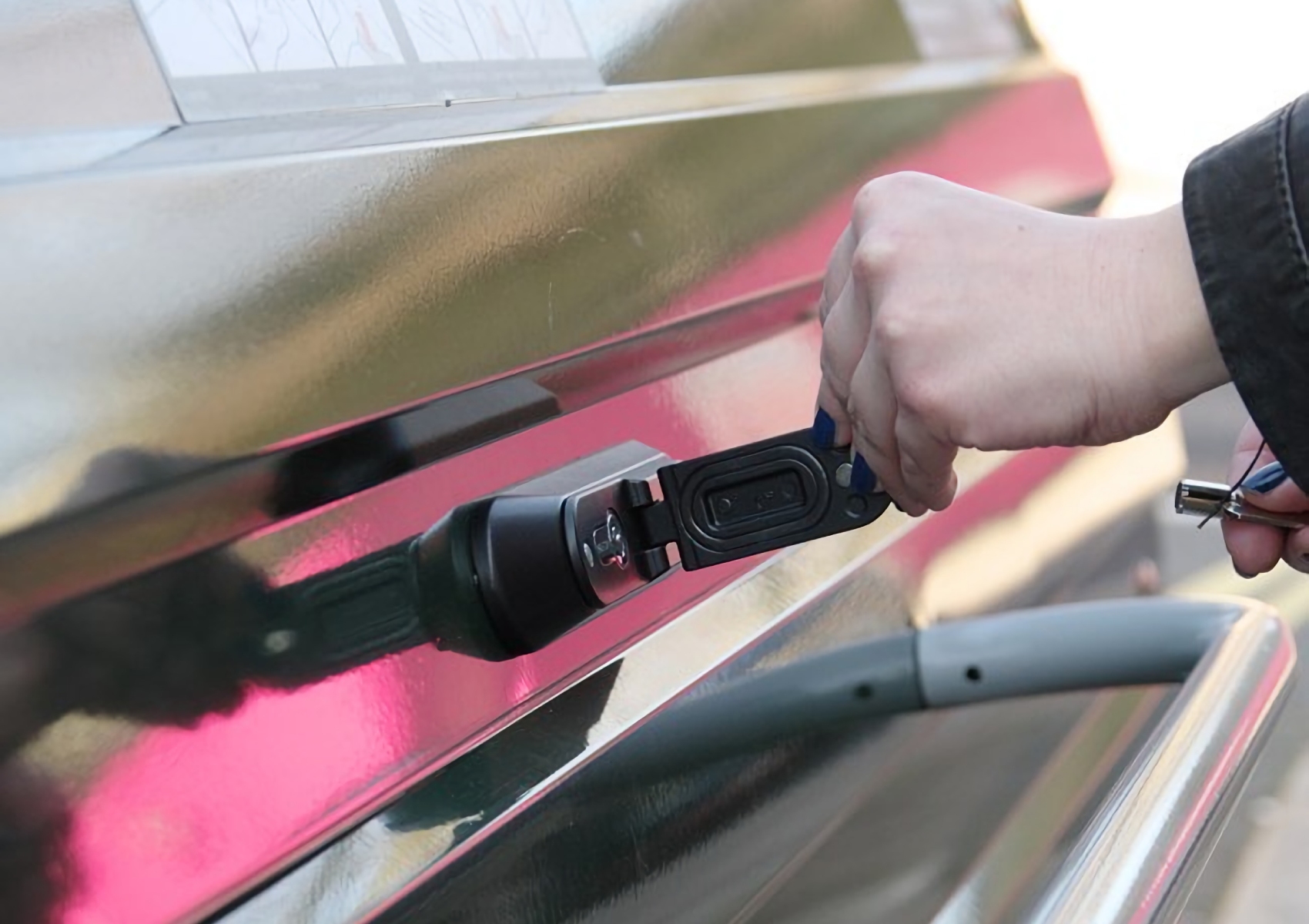
TRANSPORT JIGS
We designed and developed transport jigs to greatly reduce the risk of damage during transport. Making it easier to count parts at delivery.
We adjusted our supply chain to better manage the higher volumes, and we began buying certain parts direct from mills to manage costs. This included specialty coated steel sheet so that we could move away from a manual and quality spill prone process.
Our record to date is 150 full sets in a single month. This represents over 21,000 individual parts in a single month that are processes to create the complete assembly.
MATERIALS USED
DC01 steel sheet and plate (3mm to 10mm), steel tube and angle, pre galvanised steel, stainless steel plate, pre-coated steel sheet.
PROCESSES USED
Supply Chain Integration, Quality Assurance, Robotic welding, manual welding, laser cutting, turret punching, press brake forming, steel rolling, tube manipulation, drilling, steel hardening, powder coating and hot dip galvanizing.
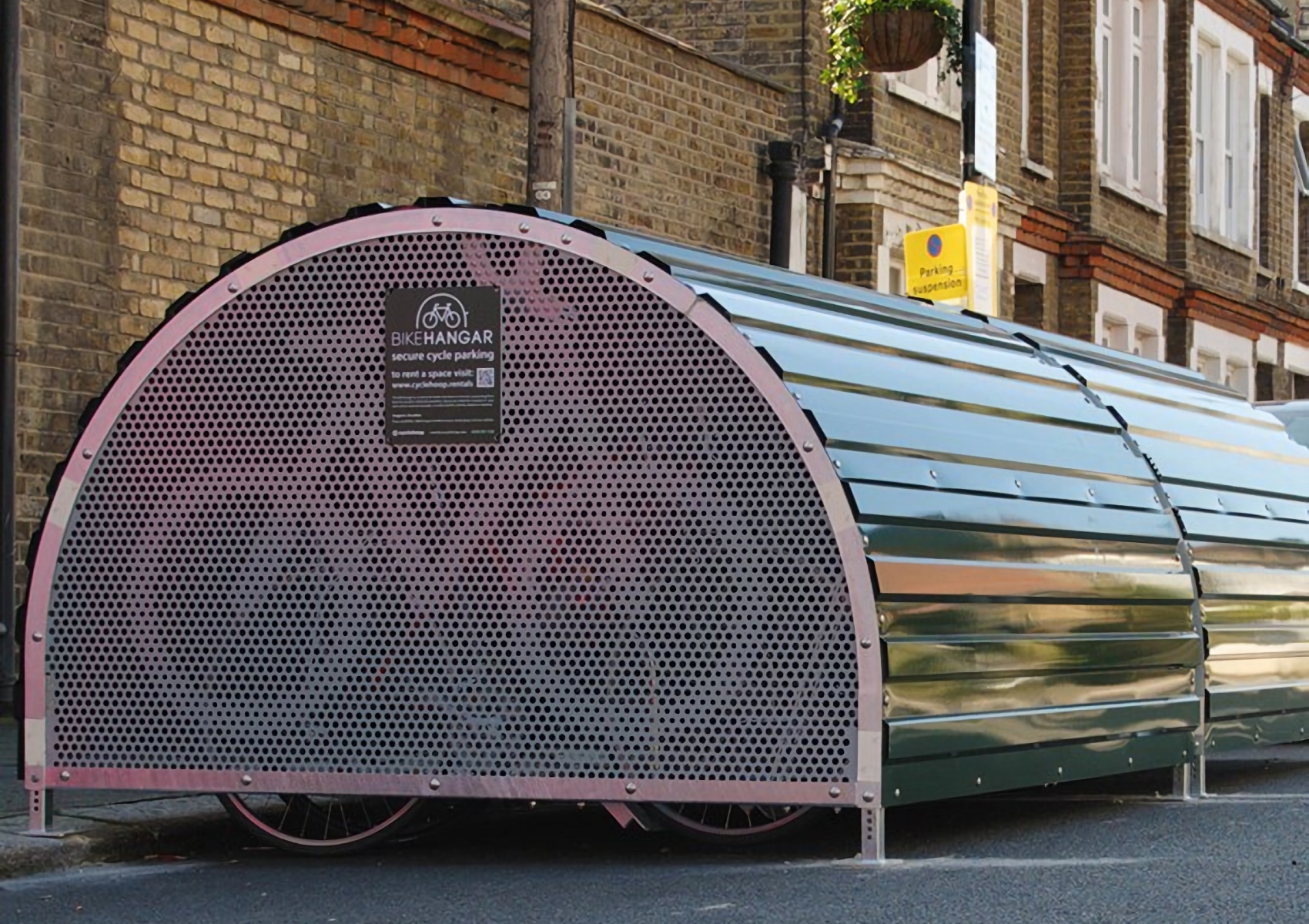
“Thank you for supporting the development of our urban bicycle enclosures. The manufacturing insight you provided during the prototyping phase has helped us significantly reduce production costs and improve the manufactured product quality. Your flexibility meant that we were able to quickly reach an excellent final design. It continues to be a pleasure to work with your team.”